Twobjshelbys originally posted the below question to Scott in the thread
http://www.fordgtforum.com/forums/showthread.php/30419-FGT-Weather-Sensitivity/page2
With an appreciative nod of recognition to our esteemed Team Member mostly associated with our GT’s suspension, Scott says he does not have first hand knowledge on the engine development topic to adequately answer the specific FGT/GT500 engine architecture program carryovers. Although I was not on the Team, my interests lie in this arena and I have over the past 10 years talked to a number of Ford engine development members and will try my best to address some of twobjshelbys questions regarding parallels between the two engine programs.
There was a fair amount of technology transfer between the supercharged 5.4L engine in the MY2007 GT500 and the FGT. Many of the same engineers worked on both programs. Obviously the overall engine architecture (supercharged 5.4L displacement) is common, including the intake charging with an integral water to air intercooler. The engine blocks are significantly different as are the block materials (initial GT500 was cast iron, FGT cast aluminum). Engine development of the GT500 engine actually started before the FGT program was finished. For those with a deeper technical interest, our FGT owners are indeed lucky that Ford allowed the engine designers the time and effort to chronicle the FGT engine design (to the best of corporate disclosure limits) in Society of Automotive Engineers (SAE) technical paper 2004-01-1252.
Some of the more noticeable differences between the two 5.4L engines are:
• Dry sump engine lubrication system with an external oil pump (FGT) vs typical wet sump oil pan on the GT500.
• The cam drivetrain was redesigned on the GT500 engine to reduce engine width for packaging requirements on the narrower Mustang engine bay.
• Forged steel Mahle connecting rods along with Mahle pistons were used on the GT500 while the FGT got Manley billet machined rods with Mahle pistons. If you have ever seen one of the connecting rods in our FGT engine, they really are a work of art. Believe we owners owe gratitude to Mr. Coletti for being a staunch supporter of a bullet proof engine design in our cars when a significantly lower priced rod option was proposed, could have been used and was ultimately rejected. Both engine programs utilized a relatively new purchasing logic of procuring an entire piston assembly (piston, connecting rod, wrist pin and circlips) from a vendor which was supplied to the Romeo engine niche line for assembly. This new process reduced complexity, improved quality/integrity and reduced system cost. Also the forged Mahle GT500 rods used a “fracture cap”design to center and align the removable connecting rod cap for assembly onto the crankshaft pin. The FGT Manley rod caps were fully machined to tolerances much tighter than those obtainable with a fracture cap design.
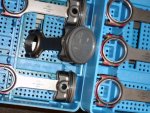
FGT Piston/Rod Assembly, Note structurally superior rod design, shot peened surface for enhanced fatigue life and dished low compression piston for supercharged intake charge.
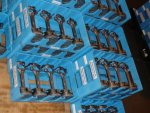
GT500 Piston/Rod Assembly.
• A “Roots” type supercharger was used on the GT500 engine while a “Lysholm” screw compressor was used for the Ford GT engine. Both compressor designs are twin rotor, positive displacement air pumps, but the Lysholm design utilizes a screw rotor design with tighter internal clearances which has been shown to be more efficient in terms of obtained boost pressure per unit of input horsepower and also lower compressor exit temperatures (less engine thermal load) than a similar Roots multi-lobe rotor design.
• Cooling water enters the side of the GT500 engine block which was a carryover from the production 5.4L engine design architecture. On the FGT 5.4L engine, cooling water enters the front of the block and uses a reverse direction water pump for increased coolant flow.
• A single fuel injector per cylinder was used on the GT500 whereas the FGT engine has two dedicated fuel injectors per cylinder.
• Cylinder block oil return runs terminate above the oil pan joint face on the GT500 engine. The same oil return runs on the FGT engine mate to return passages in the oil pan for near zero “windage” (crankshaft spinning thru the returned oil).
• The FGT engine has a structural windage tray for added block rigidity.
• The production GT500 engine used a cast iron cylinder block until 2011 which differs from the aluminum block used on the FGT engine. After 2011 the GT500 block changed to aluminum with a metallic sprayed bore material for the rings to contact. The FGT aluminum block utilizes steel sleeves for each piston to travel within. This new GT500 block shared the same basic design feature of the preceding cast iron design block.
• Because of the availability of high pressure front vehicle cooling air as the car was driven, the GT500 crankshaft harmonic damper was a less costly elastomeric damper. The FGT 5.4L powerplant due in part to its buried mid-engine location and thus higher operating temperatures used a more expensive, multi tuned viscous harmonic damper.
• And finally the GT500 engine block had open bulkhead windows while closed bulkhead windows were used on the FGT engine for added stiffness.
As to the temperature drop across the supercharger intercooler, I would estimate it to be in the 100-130°F range.
Hope this answers some of your questions.
http://www.fordgtforum.com/forums/showthread.php/30419-FGT-Weather-Sensitivity/page2
Hi Scott
I asked a similar question in the tire topic too. Over there it was about how the great amount of work on the Goodyears influenced the decision to use the same tire on the GT500
Here the question is similar. How much info sharing was done between the two teams on superchargers? The FGT used a different one, but underneath the engines were quite similar (yeah, I know, but at least for displacement and probably similar heat generation). Were design considerations on the FGT then leverged into the GT500?
Thanks!
Hi Tony,
Leveraging the FGT work, especially powertrain was SVT's intent, but I do not have first hand knowledge of the level of transfer to the GT500. I was not involved on the project and did not keep tabs on it. Mark McGowan may know.
Scott
Glad its a help. 10-4 on water injection. I am sorry, I don't have the detail intake temp data for you.
Scott
With an appreciative nod of recognition to our esteemed Team Member mostly associated with our GT’s suspension, Scott says he does not have first hand knowledge on the engine development topic to adequately answer the specific FGT/GT500 engine architecture program carryovers. Although I was not on the Team, my interests lie in this arena and I have over the past 10 years talked to a number of Ford engine development members and will try my best to address some of twobjshelbys questions regarding parallels between the two engine programs.
There was a fair amount of technology transfer between the supercharged 5.4L engine in the MY2007 GT500 and the FGT. Many of the same engineers worked on both programs. Obviously the overall engine architecture (supercharged 5.4L displacement) is common, including the intake charging with an integral water to air intercooler. The engine blocks are significantly different as are the block materials (initial GT500 was cast iron, FGT cast aluminum). Engine development of the GT500 engine actually started before the FGT program was finished. For those with a deeper technical interest, our FGT owners are indeed lucky that Ford allowed the engine designers the time and effort to chronicle the FGT engine design (to the best of corporate disclosure limits) in Society of Automotive Engineers (SAE) technical paper 2004-01-1252.
Some of the more noticeable differences between the two 5.4L engines are:
• Dry sump engine lubrication system with an external oil pump (FGT) vs typical wet sump oil pan on the GT500.
• The cam drivetrain was redesigned on the GT500 engine to reduce engine width for packaging requirements on the narrower Mustang engine bay.
• Forged steel Mahle connecting rods along with Mahle pistons were used on the GT500 while the FGT got Manley billet machined rods with Mahle pistons. If you have ever seen one of the connecting rods in our FGT engine, they really are a work of art. Believe we owners owe gratitude to Mr. Coletti for being a staunch supporter of a bullet proof engine design in our cars when a significantly lower priced rod option was proposed, could have been used and was ultimately rejected. Both engine programs utilized a relatively new purchasing logic of procuring an entire piston assembly (piston, connecting rod, wrist pin and circlips) from a vendor which was supplied to the Romeo engine niche line for assembly. This new process reduced complexity, improved quality/integrity and reduced system cost. Also the forged Mahle GT500 rods used a “fracture cap”design to center and align the removable connecting rod cap for assembly onto the crankshaft pin. The FGT Manley rod caps were fully machined to tolerances much tighter than those obtainable with a fracture cap design.
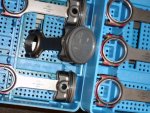
FGT Piston/Rod Assembly, Note structurally superior rod design, shot peened surface for enhanced fatigue life and dished low compression piston for supercharged intake charge.
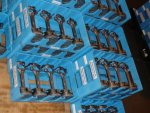
GT500 Piston/Rod Assembly.
• A “Roots” type supercharger was used on the GT500 engine while a “Lysholm” screw compressor was used for the Ford GT engine. Both compressor designs are twin rotor, positive displacement air pumps, but the Lysholm design utilizes a screw rotor design with tighter internal clearances which has been shown to be more efficient in terms of obtained boost pressure per unit of input horsepower and also lower compressor exit temperatures (less engine thermal load) than a similar Roots multi-lobe rotor design.
• Cooling water enters the side of the GT500 engine block which was a carryover from the production 5.4L engine design architecture. On the FGT 5.4L engine, cooling water enters the front of the block and uses a reverse direction water pump for increased coolant flow.
• A single fuel injector per cylinder was used on the GT500 whereas the FGT engine has two dedicated fuel injectors per cylinder.
• Cylinder block oil return runs terminate above the oil pan joint face on the GT500 engine. The same oil return runs on the FGT engine mate to return passages in the oil pan for near zero “windage” (crankshaft spinning thru the returned oil).
• The FGT engine has a structural windage tray for added block rigidity.
• The production GT500 engine used a cast iron cylinder block until 2011 which differs from the aluminum block used on the FGT engine. After 2011 the GT500 block changed to aluminum with a metallic sprayed bore material for the rings to contact. The FGT aluminum block utilizes steel sleeves for each piston to travel within. This new GT500 block shared the same basic design feature of the preceding cast iron design block.
• Because of the availability of high pressure front vehicle cooling air as the car was driven, the GT500 crankshaft harmonic damper was a less costly elastomeric damper. The FGT 5.4L powerplant due in part to its buried mid-engine location and thus higher operating temperatures used a more expensive, multi tuned viscous harmonic damper.
• And finally the GT500 engine block had open bulkhead windows while closed bulkhead windows were used on the FGT engine for added stiffness.
As to the temperature drop across the supercharger intercooler, I would estimate it to be in the 100-130°F range.
Hope this answers some of your questions.