Hello all! Some of you may not remember me as I have not posted for a long time. I bought a body in white chassis from Ford almost 6 years ago with the intention of completely building a Ford GT widebody from the ground up. Some of you have asked what happened to the project and I'm sure many thought that I gave up. But the answer to that is NO! I think about this car every day and whatever parts I can't find, I make or source, so it has been taking a little longer than planned. I thought that many of you might be having the same challenges that I did on finding parts or alternate solutions, and I am happy to share what I can. At this point I have literally put every nut and bolt on the car and have become almost too intimate with this sexy beast.
So this is where it all starts.
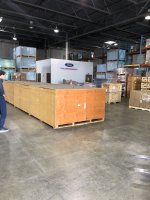
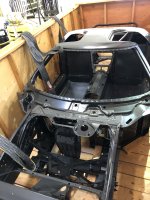
The Chassis was picked up in as a Ford part number in a crate from a Romulus warehouse. At the time, there were about 35-40 chassis left for sale. Today these are gone. The chassis is literally a body in white chassis with nothing attached to it, not even rivnuts for bolts to fasten to. When I bought this, I had no idea how hard it would be to find parts for this car. I had all of the body panels for the Ray Hoffman widebody version of the car and decided that I would go this way.
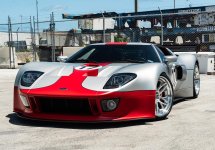
This is the Ray Hoffman car and the exact body kit that I have for mine off of the same molds. I began collecting parts and in the meantime needed to address the wide body suspension that would be required. Each of the control arms would have to be 4” longer than stock. I partnered with some of the well known GT guys along the way and was able to design and fabricate my new suspension.
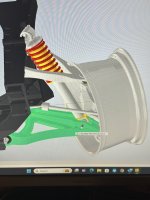
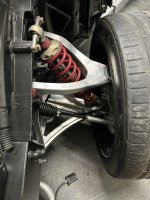
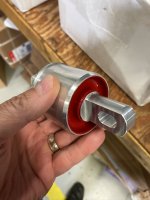
The suspension turned out great! All of the control arms are custom designed to handle a variety of tire/wheel sizes and I had to develop bushings for all of these. I decided to design these for the stock control arms so that I could go either way if I changed my mind. Instead of rubber like the OEM used, I used high performance polyurethane and experimented with several durometers to get the feel right.
Of course when extending the control arms, the tie rods had to be lengthened as well as the half shafts. I designed a half shaft extension that sandwiches between the transmission and the half shaft and I had to use an aftermarket inner tie rod end that was a little longer. An Interesting fun fact is that the Tesla Model 3 outer tie rod mates perfectly to the stock GT steering knuckle and also has the proper thread for the inner tie rod. Who wudda thunk?
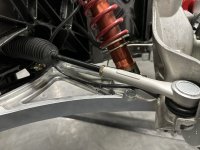
I was able to find some parts but realized that a lot of the little detail parts were going to be hard to come by or very expensive to buy one at a time so I bought a wreck that was picked over, but had a lot of the parts that I needed – particularly the interior.
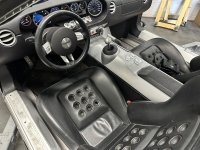
This picture is a bit of a spoiler as this is where the car is today, but most of my interior came from the doner car. I have a lot of pictures of the car at each stage so if someone is looking for some detail, I can probably dig up a picture. There is also an order of operations when putting the car together and I can tell you that I probably put this car together twice, having to take it apart because of a step that I missed previously.
Along the way there were many parts that had to be reverse engineered because of availability or known failures. Here are some examples of what I had to make.
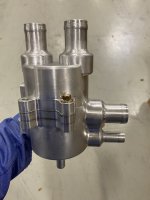
Thermostat housing that houses the stock thermostat and o-rings. This is machined, while the stock housing is cast aluminum and known to be porous and leak with age.
So this is where it all starts.
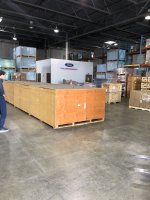
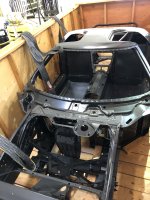
The Chassis was picked up in as a Ford part number in a crate from a Romulus warehouse. At the time, there were about 35-40 chassis left for sale. Today these are gone. The chassis is literally a body in white chassis with nothing attached to it, not even rivnuts for bolts to fasten to. When I bought this, I had no idea how hard it would be to find parts for this car. I had all of the body panels for the Ray Hoffman widebody version of the car and decided that I would go this way.
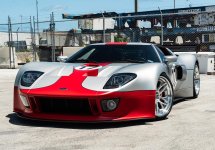
This is the Ray Hoffman car and the exact body kit that I have for mine off of the same molds. I began collecting parts and in the meantime needed to address the wide body suspension that would be required. Each of the control arms would have to be 4” longer than stock. I partnered with some of the well known GT guys along the way and was able to design and fabricate my new suspension.
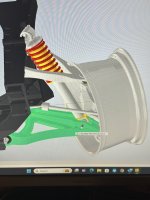
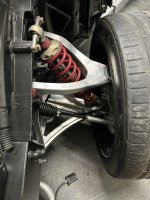
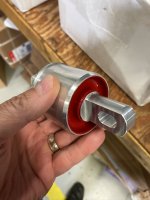
The suspension turned out great! All of the control arms are custom designed to handle a variety of tire/wheel sizes and I had to develop bushings for all of these. I decided to design these for the stock control arms so that I could go either way if I changed my mind. Instead of rubber like the OEM used, I used high performance polyurethane and experimented with several durometers to get the feel right.
Of course when extending the control arms, the tie rods had to be lengthened as well as the half shafts. I designed a half shaft extension that sandwiches between the transmission and the half shaft and I had to use an aftermarket inner tie rod end that was a little longer. An Interesting fun fact is that the Tesla Model 3 outer tie rod mates perfectly to the stock GT steering knuckle and also has the proper thread for the inner tie rod. Who wudda thunk?
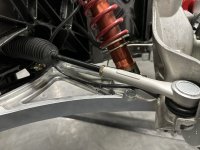
I was able to find some parts but realized that a lot of the little detail parts were going to be hard to come by or very expensive to buy one at a time so I bought a wreck that was picked over, but had a lot of the parts that I needed – particularly the interior.
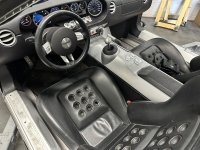
This picture is a bit of a spoiler as this is where the car is today, but most of my interior came from the doner car. I have a lot of pictures of the car at each stage so if someone is looking for some detail, I can probably dig up a picture. There is also an order of operations when putting the car together and I can tell you that I probably put this car together twice, having to take it apart because of a step that I missed previously.
Along the way there were many parts that had to be reverse engineered because of availability or known failures. Here are some examples of what I had to make.
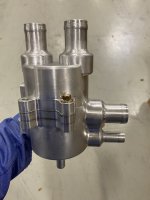
Thermostat housing that houses the stock thermostat and o-rings. This is machined, while the stock housing is cast aluminum and known to be porous and leak with age.